BSc. & MSc. Theses / Semester Projects
BS & MS students are encouraged to contact us directly regarding possible thesis topics. We usually tailor the topic to a student's particular interests. This involves the nature of the work (theoretical, computational and/or experimental) as well as the project context (fundamental science or application-oriented in automotive, aerospace or civil engineering). Short stays on the premises of our industrial or academic partners can also be integrated in the scope of your thesis work in our lab. Kindly contact Prof. Mohr or Dr. Roth directly. A few examples of available topics are given below.

The failure of rotating jet engine components is a dramatic event which must be prevented by suitable design measures. Due to the elevated temperatures and high loading speeds involved, new experimental techniques must be developed to characterize the failure response of jet engine materials. It is the goal of this project to design and perform new experiments that provide insight into the stress state dependent failure response of super alloys at high temperatures and high strain rates. Interested candidates will also have the opportunity to carry out finite element simulations of extreme loading events.

A main outcome of our combined numerical-experimental research is a comprehensive experimental program for characterizing the effect of stress state on ductile fracture initiation. The next step is the full automation of the testing system to be available to generate an unmatched wealth of experimental data for all relevant steel and aluminum alloy sheets that are used in automtive engineering today. The candidate will have the opportunity to program our universal robot to perform basic mechanical experiments.

The determination of the strain to fracture for pure shear loading is an important unresolved challenge in solid mechanics. We have recently developed through computational optimization. The goal of this project is to demonstrate the validity of the new shear specimen through careful experiments on many engineering materials. The project provides the opportunity to learn the latest experimental techniques for monitoring strains and cracks in specimens including high speed photography and scanning electron microscopy. At the same time, it has the potential for major breakthrough if the validity of the experimental results are confirmed for multiple materials.

In sheet metal forming, it is often assumed that the strain to fracture depends on the sheet thickness. However, this assumption is in contradiction with basic theory. It is the purpose of this project to clarify this issue using a combined experimental-numerical approach. The work will involve designing and executing a meaningful experimental study. The candidate will have the opportunity to reach an expert level non-linear finite element analysis and to acquire basic skils in experimental mechanics.

We are constantly developing new mesostructures for porous materials to achieve special mechanical properties such as exceptionally-high specific impact energy absorption. The resulting metamaterials are manufactured at different lengh scales using different 3D printing techniques. To gain detailed insight into the governing deformation mechanisms, the mechanical experiments on nano- and micro-architetured are performed inside the chamber of a scanning electron microscope. It is the goal if this project to design and execute compression experiments on nano-architectured lattice materials and to compare the experimental results with numerical simulations.

With the help of a recently-developed micro testing technique we are now able to perform fracture experiments on miniature specimens. In the framework of this project, we will make use of this new technique to characterize the plasticity and fracture properties of potentially-harmful flying objects with dimensions of less than a few millimeters. Depending on the interest and motivation of the student, the experimental program may be carried our under static and/or dynamic loading conditions.

In Split Hopkinson Pressure Bar (SHPB) experiments, a specimen can be strained by 100% in a few micro seconds. Even though we are using rather small specimens, very high forces build up during the experiments that require special specimen clamping systems. It is the purpose of this project to develop and validate a new clamping system that prevents the slip of advanced high strength steel specimens under severe impact conditions.

Some classes of materials such as thermoplastics possess a mechanical behavior that is highly dependent on the sample temperature during the test. The precise control and measurement of temperature is then paramount to precisely model the mechanical behavio. In this project, the student will develop a heating and cooling system that can be integrated in a range of automated testing systems. The system will be controlled with a LabVIEW program that will be implemented within the automated testing machine core program. The system will then be tested on thermoplastics samples.
For more information, please contact .
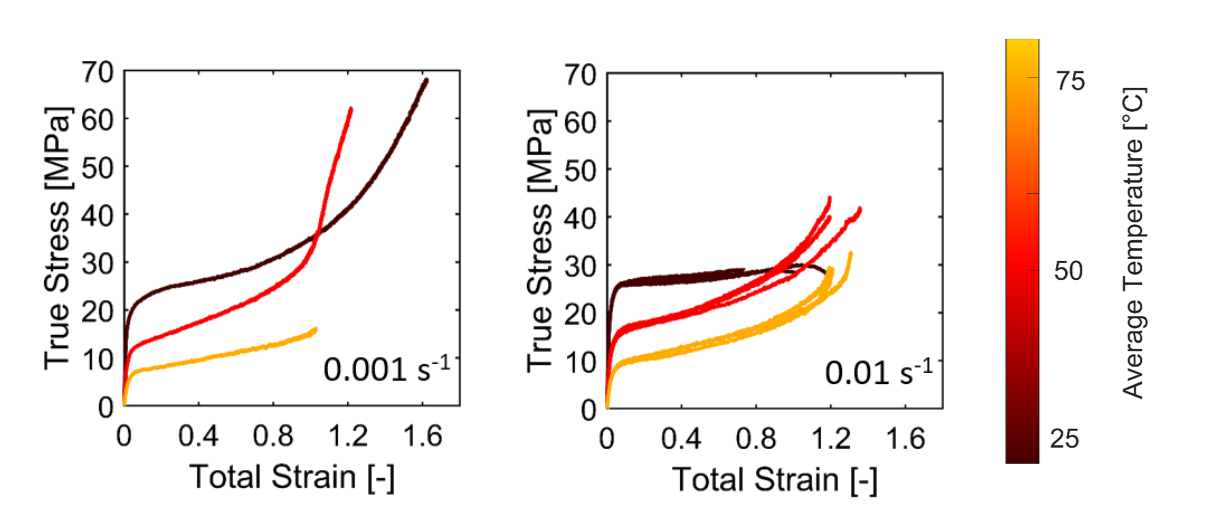
Taking advantage of the recent development of automated machines in the laboratory, the project aims at expanding the investigation of thermoplastics mechanical behavior to various stress states. The student will use pre-existing sample geometries to test thermoplastics at different temperatures and strain rates on different testing machines. Comparison of the test results with FEM simulations will be used to validate the sample geometry to obtain the desired stress state.
For more information, please contact .
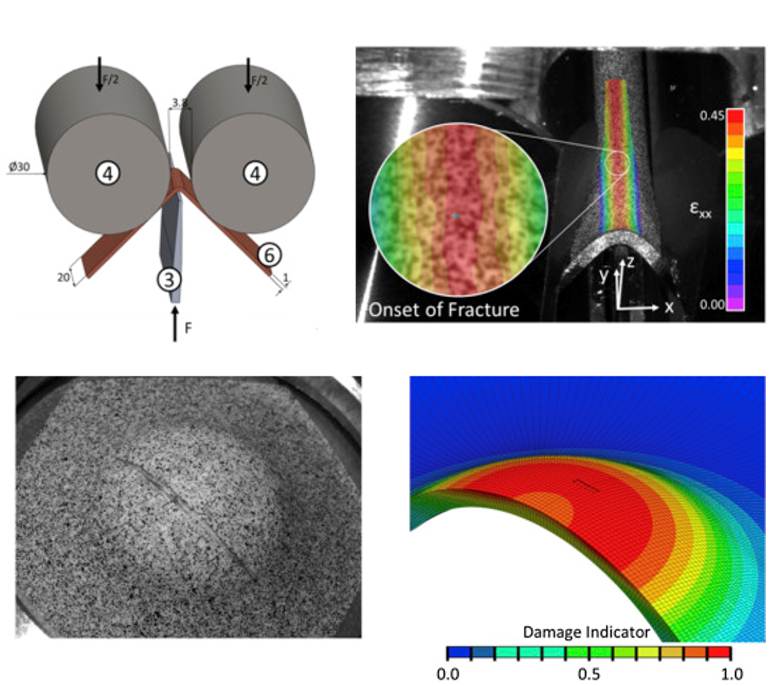