Ultralight Design
In-page quick links:
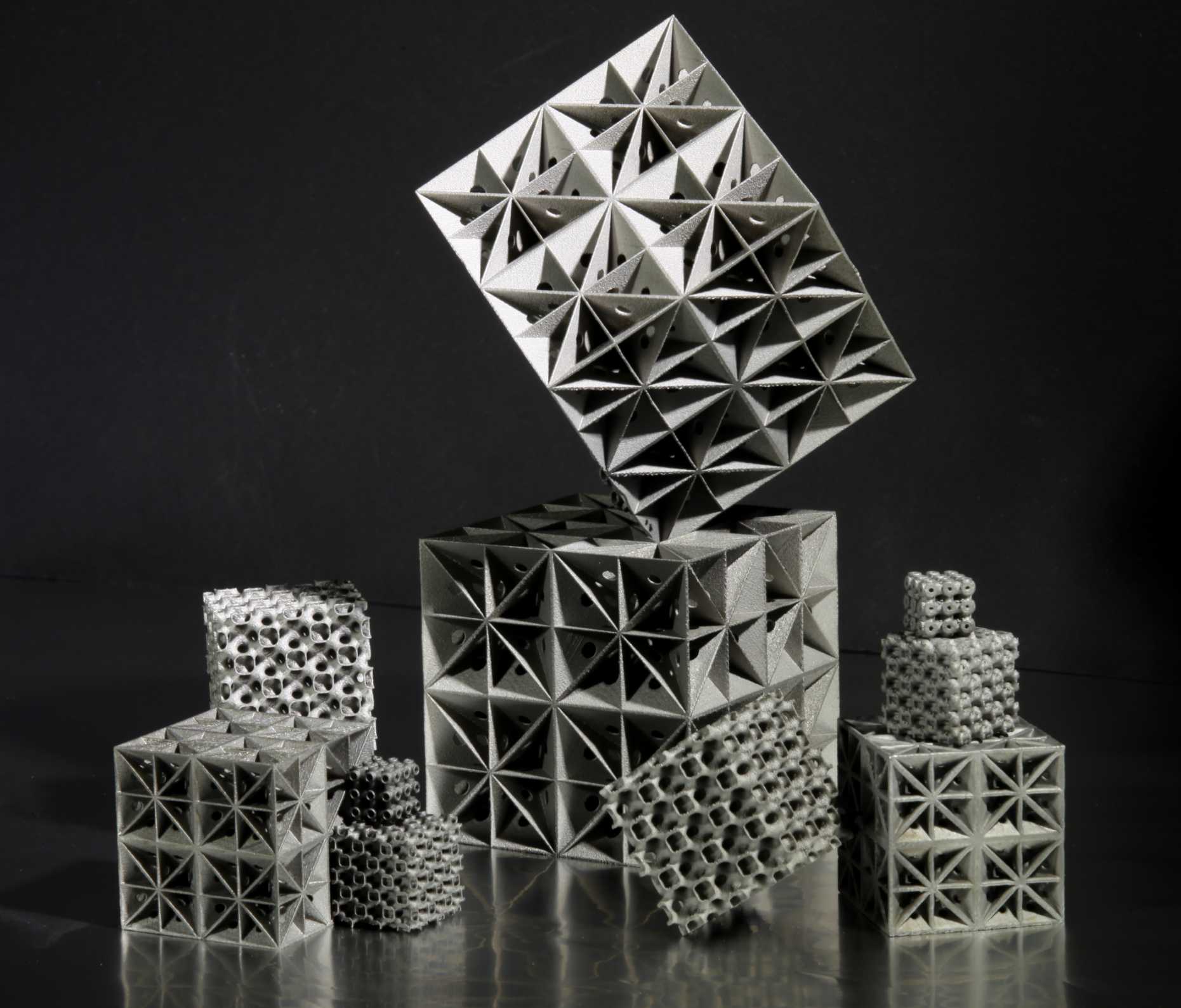
- Three-dimensional metamaterials can be designed using different building blocks depending on the targeting applications. Historically, beams have been used to generate truss lattices resembling civil engineering constructions or atomic lattices. To improve mechanical properties, we design metamaterials based on smooth shells or flat plates. The former, design to minimize local curvature exhibits high energy absorption capabilities due to its smooth nature. On the other hand, plate lattices can exhibit optimal stiffness and near optimal strength. Our research shows that the nature of the building block is crucial to the mechanical properties while the symmetry groups have a less important role. Further improvements in mechanical properties can be obtained by tailoring the building block shape to specific applications. These findings hold true independently of materials used for the manufacturing of the metamaterials.

Numerical simulations are used to investigate the effect of various design parameters and validate analytical model. Due to the periodic nature of the metamaterials, numerical simulations can be carried out at the unit cell level (i.e. minimal translational unit) using periodic boundary conditions. The video below shows the hydrostatic compression of a hollow-tube and sphere lattice with an FCC symmetry.

Low Strain Rate Experiments
The video shown below presents the uniaxial compression of a stainless steel plate lattice at slow compression speed. Due to the presence of very thin plates, plastic buckling is observed and the specimen deforms layer by layer.

High Strain Rate Experiments
The video below shows a compression test of an additively-manufactured truss structure in a direct impact setup. The experiment lasts for ~1.4 ms (milliseconds), which corresponds to the duration of a typical photo flash strobe. High speed photography helps us in making such short events visible, unraveling the mechanism at play - in the present case the very steady and uniform deformation of the newly developed structure.

Selective Laser Melting (SLM)
Selective Laser Melting (SLM) is a powder bed fusion technique that is widely used in the field of additive manufacturing. It is used to manufacture samples from (stainless) steels as well as titanium or aluminum alloys. The picture below shows smooth shell lattices made from stainless steel 316L with an edge lengths ranging from ~96 mm to ~23 mm.

Direct Laser Writing (NanoScribe)
While additive manufacturing techniques liek SLM can produce lattices up to tens of centimeters in height, the largest design freedom is obtained using micro/nano fabrication techniques, such as two-photon stereolithography. On top on this, many post-processing methods can be used to create ceramics or metallic micro-lattices. Due to their small scale, they leverage unusual material properties such as ceramics ductility or exceptional strength of metals.

Composite Materials
Fused deposition modelling (FDM), a growing additive manufacturing methods is used in printing of fibre-reinforced composites at the scale of the centimeter. The presence of the fibers provides additional stiffness and strength to the structure.
